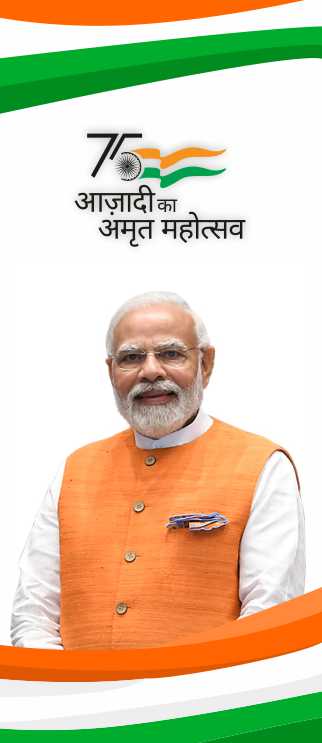
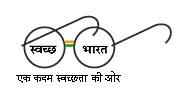
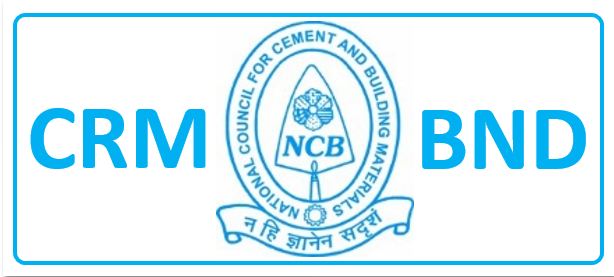
News & Events
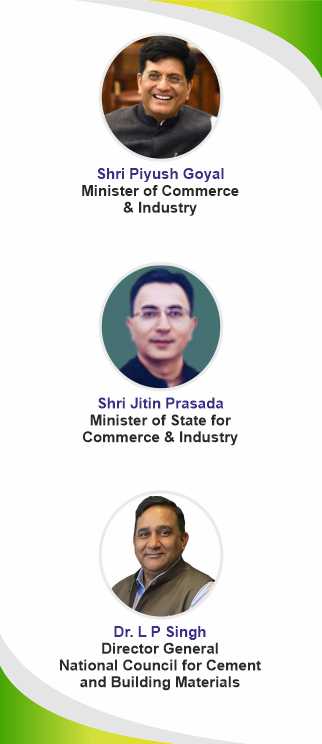
News & Events
- Tender Notice-Upgradation of the Industrial Shed in NCB Campus, Ballabgarh, Haryana on EPC Mode
- Written test and Personal discussion against the Advt. No. R/05/2025 (01) on 09-10th September 2025 at NCB Ballabgarh
- Result for Round II & Spot Admission of One Year PG Diploma in Cement Technology (2025-26)
- Notification for engagement of Apprentices for the year 2025–26 for NCB-Hyderabad Unit (Receipt of Applications - Last Date 19.08.2025)
- Admission Notice - Round II & Spot Admission of One Year PG Diploma in Cement Technology (2025-26)
- List of Selected Candidates of One Year PG Diploma in Cement Technology (2025-26)
- Letter & List of Shortlisted Candidate for Written/Interview of One Year PG Diploma in Cement Technology (2025-26)
- NCB IC Event: Innovate Youth: Building Tomorrow's Entrepreneurs.
Consultancy services for getting NABL Accreditation as per ISO/IEC 17025:2017
Notice on Public Grievance
NCB – CCE EVENTS / Forthcoming Training Programmes
Proficiency Testing Schemes
NCCBM to host 17th International Congress on Chemistry of Cement (ICCC) in 2027 in New Delhi
Thrust Areas
THRUST AREAS OF ACTIVITIES
Establishing Limestone Consumption Factor (LCF) for cement plants
Limestone consumption factor studies are very important from the point of view of rationalization of limestone consumption in the production of cement, estimating royalty payable to the state for the limestone mined from their respective captive mines besides internal material audit of the concerned cement plant. NCB has carried out limestone consumption factor studies for cement plants from all over the country.
Evaluation of raw materials and cement samples
The cement industries are facing challenges in national and global perspectives in international trade and commerce. This fact brought about awareness and emphasis on:
- Improved grades of cement for construction
- Utilization of wastes and industrial by-products in cement manufacture
- Conservation of resources and protection of environment
- Export of cement and Competitiveness meeting quality requirements and consumer orientation\
In order to assist the cement industry in its endeavor to make available quality cement to the consumers, NCB has evolved scheme for “Evaluation of raw materials and cement samples package annually as a diagnostic tool and feed back on their quality to the plant management. In addition, routine testing and evaluation of other materials such as by-product wastes, aggregate, concrete etc is carried out as part of services rendered to cement and construction industries
Optimization of Raw Mix Design for cement manufacture
Studies on optimization of raw mix design for producing OPC clinker of desired quality and maximization of blending component etc are taken up both for operating cement plants as well as for Greenfield cement projects with following objectives:
- Improvement in clinker quality
- Improvement in cement performance
- Utilization of low grade/ waste materials as component of raw mix
- Evaluation and utilization of raw materials from different sources
- Design of alternate mixes for use with coal/ petcoke from different sources
Refractory Engineering Services
Refractory still remains one of the important inventories of cement plant. The estimated requirement of various refractory materials such as bricks, castables, mortars, insulations, blankets, ropes, ceramic wool, etc. for one million tonne green field project is around 3000 MT. Further, refractory related problems have major impact on the economic and technical health of the plant and therefore, following areas of refractory are important for investigations:
- Study related to quality of refractories
- Study related to installation of refractories
- Performance / lining life of refractory
- Establishing the bench mark for performance indicators Scope for further improvement
NCB has carried out technical audit of refractory and practices of installation by cement plants and could identify the areas which require attention for improved performance including longer life.
Investigations on kiln shell corrosion
Corrosion of kiln shell is influenced by a number of factors such as composition of the metallic shell and its environment, temperature of the shell, cleanliness and roughness of the shell surface and its contact with other materials, oxidizing/reducing conditions, improper combustion of coal, etc. The corrosion phenomenon takes place mainly due to the presence of sulphates and chlorides of alkalis and calcium at high temperature in the cement kiln. The role of refractories in cement kiln is primarily to protect the steel shell from the direct attack of deleterious gases and clinker melt and to reduce the shell temperature so that steel of the shell does not loose its properties. The reduction in shell temperature also leads to energy conservation besides providing workable conditions near kiln shell.
Clinker melt deposit on side walls of bricks
Metallic deposit on one side of brick
NCB has carried out number of investigations and found that the areas such as the passage of volatiles through body of bricks and gaps/joints in the refractory lining needed to be reviewed for improvement particularly in terms of the quality of bricks and the installation practices. This could result in preventing and minimizing the phenomenon of shell corrosion. NCB has also suggested remedial measures to control kiln shell corrosion.
Studies on coating and ring formations
Build ups and ring formation in cement rotary kilns has been known to induce operational instability and restrict gas/material flow to the point where kiln has to be stopped. Studies on coating and ring formation are taken up as a part of the diagnostic studies for minimizing/ eliminating coating and ring formation in cement rotary kiln system. The studies involve chemical and mineralogical evaluation of raw materials being used by the plant, evaluation of raw mix from periods of normal operation as well as from periods preceding ring/ coating formation and chemical and mineralogical evaluation of coating and ring samples. Recommendations have been found important on modifying the raw mix designs for avoiding coating/ ring formations.
Heavy coating in transition zone
Breaking of coating in transition zone area
Latest Activities
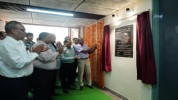
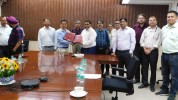
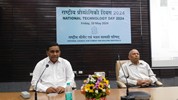
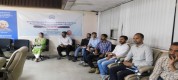
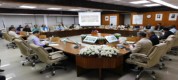
          Click to view more>>           Click to view more>>               Click to read more>>                Click to read more>>                    Click to read more>>